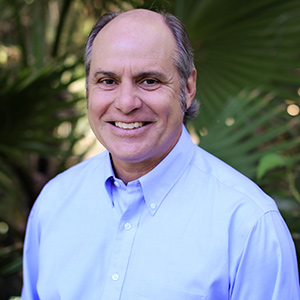
Dave Umstot
Long before Dave Umstot founded the award-winning Umstot Project and Facilities Solutions, LLC in La Mesa, Calif., he oversaw the herculean $1.6 billion Proposition S & N capital bond program at the San Diego Community College District. As vice chancellor of facilities management from 2007 to 2013, Umstot was also responsible for facilities maintenance, grounds and custodial operations, parking, and school police for the district. And if that wasn’t enough of a challenge, in 2008 the global economy collapsed.
California’s government funding for community colleges was severely reduced, and the SDCCD had to navigate its massive voter-approved expansion (1.6 million square feet) with operating budgets that were reduced 16 percent over a three-year period.
“We quickly realized we could not continue business as usual and meet our obligations to our students, faculty, and staff within these constraints,” said Umstot. “So we embarked on a Lean journey in our Facilities Services (maintenance, grounds and custodial) organization in 2009 to improve our quality of service and reduce our costs. The SDSU Lean Enterprise program was a great fit that allowed us to send two cohorts a year for three years to help build Lean understanding among our director, supervisors, regional facilities officers, and planners. These individuals in turn became internal champions on our Lean journey.”
Umstot answered a few questions about that journey through SDSU’s Lean Enterprise program.
How did the Lean process unfold at the San Diego Community College District?
We established learning teams in our capital project delivery core team to share and develop Lean knowledge including reading books together, implementing A3 problem-solving, using value stream and process mapping to eliminate waste, improve flow, and add value for our constituencies which included the students, faculty, staff, and taxpayers. You can download a paper that captures metrics of our efforts that was presented and published at the 2014 International Group for Lean Construction annual conference in Oslo, Norway.
Can you give an example of a practice or procedure that was changed or streamlined?
There were numerous things we did as a result of integrating Lean enterprise into our work flow including focusing on stopping doing things we should not be doing, standardizing things we were doing well, and implementing new things that we should be doing. We had two overarching metrics we used to benchmark our starting point and where we wanted to go with a new business model. These were increasing the square footage cleaned by our custodians from 13,900 to 25,000 and reducing our maintenance costs from $3.93 to $2.25 per square foot over a three-year period. Between 2009 and 2012 we increased our custodial square footage to 21,225 and our maintenance costs had been reduced to $2.31 per square foot. In fiscal year 2011/12, this resulted in a cost savings of $4,553,063. These results were the cumulative effect of many smaller changes and improvements in the way we delivered our services. It should be noted that the district has continued to make even more progress toward these goals that has exceeded the initial goals.
Were employees who went through SDSU’s Lean Enterprise program eager to spread the gospel of Lean?
We certainly developed internal champions from the program, but equally important was that we negated attitudes that might have undermined the efforts if they did not understand what we were trying to do and why. As a public agency, it was important to get employees engaged and bought in to the process. There were naysayers that could have effectively made it difficult to implement organization-wide, but by going through the program, they developed an understanding of what we were doing, why and how. This was a key in getting Lean enterprise integrated into our business model across our geography and various departments.
Did you actively seek out contractors and subcontractors who were Lean certified?
It is important to understand that there is no certification that applies to capital project delivery directly. What we did do was integrate contractors’ and specialty trade contractors’ knowledge and practice of Lean enterprise into our selection process for awarding contracts. We also adopted universal use of the Last Planner(R) System based on pull production to manage the activities and schedules of our capital projects during construction. There is a great paper on how the Last Planner system is the gateway to Lean behaviors that was written by one of our firm’s principals, Dan Fauchier, in concert with Dr. Thais Alves at San Diego State University’s College of Engineering.
What do you think are the biggest strengths of SDSU’s Lean Enterprise program?
Instructors with world-class experience, and hands-on learning coupling theory with doing.
How feasible is it for full-time employees to take the program?
This requires leadership in an organization to understand that this release time for employees to participate is an investment that will reap rewards several times over. People represent the single largest expense for many organizations, and giving them the knowledge and power to improve how they do their daily work can lead to wonderful things if the organization is committed to allowing them to practice what they have learned.
Do you think employees from every industry can benefit from Lean training?
Absolutely yes, provided their organizations are willing to support them in applying what they have learned in the workplace. I want to stress the importance of this, because we often see organizations that send people to training, delegate it, and then expect things to change when they are not supportive of change in the organization. Leadership from the executive level on down is necessary for this to have the greatest benefit. Without it, employees will get frustrated and the organizational leadership loses their support and the potential benefit of the training.
Tell us about your company, Umstot Project and Facilities Solutions, LLC.
The overarching theme for everything we do is “helping deliver better projects, performance and results.” We have worked with more than 40 organizations since 2013 including private sector owners, public sector owners, developers, hospitals, universities, builders, specialty trade contractors and nonprofit organizations in a variety of capacities helping them achieve just that. You can learn more about us at www.umstotsolutions.com and our affiliate company, The ReAlignment Group of California, LLC at http://leancalifornia.com/.
Do you find yourself applying Lean principles in your everyday life?
Absolutely, and there is always room for continued improvement.