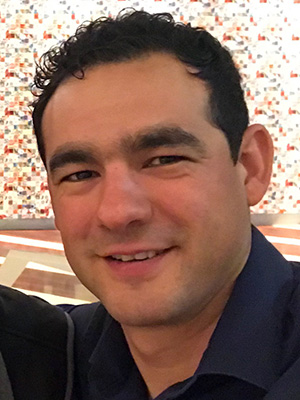
Jorge A. González Ayala
As a Lean Six Sigma Master Black Belt at Solar Turbines, Jorge González Ayala enrolled in the Professional Certificate in Lean Enterprise program at SDSU’s College of Extended Studies, with the expectation to later teach some of the concepts, as required by his role as facilitator.
“I was hoping to go deep into the technical aspects of Lean in the form of measurements and even some Six Sigma statistical tools,” said González Ayala. “What really happened is I ended up meeting a set of very talented practitioners of Lean in transactional and manufacturing processes. The interaction with employees of other organizations was priceless in the sense that it brings a window to how things trend to break down everywhere, but processes can be fixed.”
González Ayala holds a degree in psychology from the Universidad Autónoma de Nuevo León, and an MBA from the Universidad Regiomontana — both in Monterrey, Mexico. He has more than a decade of experience as a human resources generalist in Mexico and California, and a focus on continuous improvement facilitation for the past 1.5 years. Regarding his Master Black Belt, González Ayala said, “I’ve heard all the jokes about the title. It’s a great conversation starter to get people thinking about continuous improvement. I must have handy examples to talk about Lean, Six Sigma, Agile or whatever is needed to make your work easier.”
González Ayala felt the biggest strength of SDSU’s Lean Enterprise program is the “access to companies practicing Lean and Six Sigma at different stages of their journey.” Every semester of the 12-week program, four classes take place off-site at three different companies so that students can see Lean in action, and connect the dots to what they’re learning in the classroom.
“We had the fortune of visiting Costco’s distribution center,” said González Ayala. “The experience was inspiring for me. It’s a wonderful tale of grassroots movement in Lean and Six Sigma. Teamwork was visible with recognition, gratefulness, and smiling people everywhere … People came first, yielding quality, velocity, and efficiency in cost.” He was also impressed that after years of Costco’s “artisanal way” of managing inventory with high levels of accuracy, they were taking it a step further with the implementation of a GPS location service.
González Ayala cited another strength of the SDSU Lean Enterprise program as the “world-class” instructors, and offered special thanks to Tracy O’Rourke, Sammy Obara, Mike Osterling and Joe Colarusso.
Shortly after completing the program, González Ayala began implementing what he had learned, at Solar Turbines.
“I developed a set of topics to conduct a Rapid Improvement Workshop, experimenting and continuing to learn. I tried two-day workshops separated in time, and it doesn’t work. Lesson learned,” he said. “Then I tried two-day workshops with two teams working on different projects. You need two facilitators … Finally, I tried a three-day workshop with one team and one value-stream map exercise, and the team was able to get Define-Measure-Analyze-Improve in a little under 24 hours of very focused, value added work. The teams still have an uphill battle implementing their ideas and adjusting to real-world demands, but it is very rewarding and relaxing when they get it to sustain.”
Not surprisingly, this Master Black Belt in efficiency also applies Lean principles in his daily life.
“We recovered square footage at home using 5S,” said González Ayala. [Editor’s note: 5S is a workplace organization method from Toyota’s original Lean manufacturing revolution. It translates from the Japanese as sort, set in order, shine, standardize, and sustain.] “I own my calendar and do one thing at the time, reducing stress, and I get to encourage people to improve their own working conditions. I love my new job.”