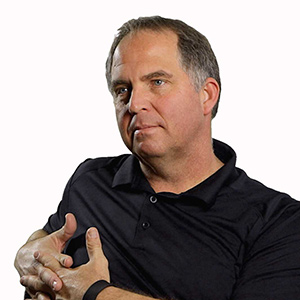
Scott Crowley, Chief Operations Officer of Lloyd Pest Control
In the 1930s, San Diego’s downtown construction boom set off another kind of boom — rodents. Their trail of destruction in warehouses and businesses caused many a panicked proprietor to call Lloyd Pest Control, which at the time was simply James Albert Ogle. His weapon of choice was a .22 caliber rifle loaded with bird shot. Ogle’s aim, diligence, and desire to discuss results and strategies for improvement with his clients led to exponential growth for the business.
Today, three generations later, Lloyd Pest Control covers Southern California with more than 200 radio-dispatched trucks, 200 licensed technicians, supervisors, a quality control staff, an entomologist, and a biologist. And Ogle’s philosophy of continuous improvement is alive and well.
Lloyd Pest Control has been sending employees through the Lean Enterprise Professional Certificate program at SDSU’s College of Extended Studies since 2013. Chief operations officer Scott Crowley was among the first to go through the program. He shares how the Lean philosophy of improving quality while decreasing costs has influenced this family-owned business.
How did you find out about SDSU’s Lean Enterprise program?
Chris Wellons from Taylor Guitars is in my Vistage group and he had talked about it at a couple of our meetings. [Vistage is an executive coaching organization with locations worldwide.] I approached him to see if he thought we could benefit — at the time I thought it was primarily a manufacturing industry tool (and they are definitely manufacturers!), and Chris let me know that he was of the belief it could definitely help us.
Yes, people often think Lean applies only, or mostly, to manufacturing processes. Can you speak to that?
While I think that Lean is certainly a great tool for manufacturing, the principles and concepts are easily adapted to just about any type of business. The Lean processes by which organizations can identify bottlenecks, for example, can be applied to just about anything — processing of documents, completion of a work day for our route technicians, etc. Kaizen events can be held to review just about any process, manufacturing or otherwise. We’ve held half a dozen here that have helped us tremendously and we are definitely not in manufacturing!
What does a Kaizen event look like and did the course teach you how to conduct one at your workplace?
We have each branch office select candidates whom they feel will be willing to actively participate AND are comfortable or familiar with the topic we’re trying to address. For example, they would not send me a termite technician to help us address smoother route completion, as they don’t work on routes in the same manner. We determine the size of the event based on the particular topic, and yes, we were guided by the Lean course in how to proceed. Also, one of the gentlemen that was attached to our group in my Lean course had a lot of experience in conducting these where he worked. He came out to us and ran the first one so we got to experience one in person.
Do employees come back eager to spread the gospel of Lean?
We have found that the concept has been very well received and have encouraged those who have taken the class to be active in their offices with what they’ve learned. Corporately, we’ve made a practice of discussing Lean on many levels and have included a wide range of employees in our Kaizen events. I’m not blind to the fact that some employees still think Lean is about thinning our ranks, but all of us who have participated in the classes have been very willing to discuss the topic with all employees and to practice the concepts whenever possible.
Have employees come to see that Lean is not at all about thinning ranks?
I would say for the most part. One of the reasons we’ve so actively involved the field staff in the Kaizen events is to give them exposure to the process so they can be educated a bit in Lean as well as participate in the event. Everyone that has participated in a Kaizen event has also received from us a copy of the book “2 Second Lean” as a means of giving even more information on the topic.
Can you give a specific example or two of a practice or procedure that was streamlined by the application of Lean principles?
Probably the two that were most prominent were the reshaping of our pest control routes and adjusting the way we’re scheduling work for our technicians from the Call Center. The former example was put into place after the first Lean course in 2013 and we’ve definitely seen our routes become more profitable. A lot that went into that project (evaluation of down time, travel time to routes, nonproductive versus productive stops, etc.) but we’re in a better place on that front now. As far as the scheduling project, that’s continuing to evolve as we play with different pieces, but the goal was to make the scheduling of work smoother and easier, reducing the number of calls between staff required to get work on the books, and we’re making progress on that front as well.
What do you think are the biggest strengths of SDSU’s Lean Enterprise program?
The variety of different topics/aspects taught over the 10 weeks definitely allows companies to seize on the places that can most readily be applied to their operation. Also, the variety of teaching perspectives brought in by the different presenters.
Can you speak to the caliber of instructors?
We all felt that the presenters, across the board, brought a very appreciated variety and breadth to the course. They all did a great job and were able to display their expertise in the field.
How feasible is it for full-time employees to take the program?
We had no trouble carving out the time. That isn’t to say that individual attendees didn’t face challenges from time to time relative to taking care of work-related items, but these worked out well for us. That includes the fact that several of our attendees came down from Riverside and Orange County to participate AND that May-June is right at the beginning of our busy season!
For more information on the Lean Enterprise Professional Certificate program at SDSU’s College of Extended Studies, please visit neverstoplearning.net/lean.