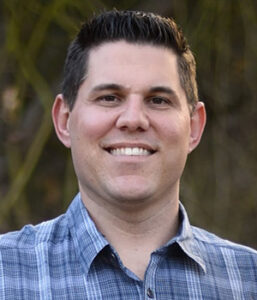
Brian Slye
As the manager of optics manufacturing and reclaim programs at Cymer — a crucial behind-the-scenes component of likely every computer chip you use in life — Brian Slye is responsible for developing cost-reduction strategies and executing projects to qualify new parts for reclaim. To amplify his ability to do just that, Slye enrolled in the Lean Enterprise Professional Certificate program at SDSU’s College of Extended Studies.
“I wanted to learn more about how to eliminate waste in a production environment, as well as in processes used throughout the company — administrative, etc.,” said Slye. “SDSU’s program came highly recommended by the senior management at my organization due to the expertise of the instructors, and for the site tours at several local companies.”
The latter proved to be Slye’s favorite part of the program. “Site visits offer an excellent way to see the concepts put into use by some of San Diego’s most important companies. I was able to take several ideas and concepts I saw at these companies and put them into use,” said Slye. “The most successful example is a continuous improvement program at Costco Optical Lab which empowered employees to submit ideas and have them reviewed and implemented by a team of actual employees. I implemented a very similar program that has now been adopted across the entire company, resulting in over 250 improvements implemented in 18 months.”
Slye answered a few questions about SDSU’s Lean Enterprise program and his career.
Please give us a brief overview of your education and career.
I graduated in 2004 with an electrical engineering degree from Cal Poly, San Luis Obispo, and went to work in the defense industry as an electrical engineer at REMEC Defense & Space in San Diego, CA. After five years, I transitioned to program management to gain a broader experience across a larger number of projects. During the next couple years I realized that my passion was for operations management, and I chose to pursue an MBA at SDSU in order to enhance my career prospects. I chose the SDSU evening program because it was the best fit for my schedule while working full time, and concentrated in finance because a financial background has been (and will continue to be) the most useful to me as I advance in my career.
Tell us a bit about Cymer.
Cymer is the largest supplier of deep ultraviolet (DUV) light sources used by chipmakers and hardware manufacturers to pattern semiconductor chips which are used in cell phones, tablets, smartwatches, and the next generation of electronics. Cymer has over 2000 lasers worldwide which are used by companies like Samsung and Intel, and chances are that nearly every computer chip you use has at least several layers printed with a Cymer laser.
Can you give an example or two of the improvements you implemented as a result of the Lean program?
One example is that we were using a separate leak-test fixture for a module which was essentially the same as the cover we use when the part ships. So, we qualified the use of the shipping covers to provide the seal necessary when performing the leak test, saving about 20 minutes per unit to install the leak fixture, and then de-install it so we can put on the shipping cover. We make maybe five or six a week, so it saved an hour per week.
We’ve also implemented several safety improvements such as more ergonomic workspaces and lifting aids for heavier modules that must be installed in the laser.
Can you speak to the caliber of the instructors?
The classroom instruction was excellent, driven by the real-world experience of the instructors — most of whom had a long career in the operations management field. The exercises for creating and using value stream maps and process maps, for example, were very effective — the instructors were able to guide the exercise as if they were consulting on a lean project at a company. This showed me how to lead these exercises within my own company to effectively run my own lean projects.
Did you have any “aha” moments in the classroom or on the site visits?
My “aha” moment in the Lean course was the realization that the tools used can be applied to all types of work environments — not just manufacturing. Value stream maps and process maps can be employed in office environments to identify choke points and cut cycle times for administrative processes just as easily as they can be applied in a manufacturing environment. Waste exists in all areas of a company, and improvements can always be made.
Did you gain any insights from your classmates — employees of other organizations?
Having classmates who are professionals in San Diego industries not only creates a great networking opportunity, but it also provides an excellent chance to gain insights into their organizations. For example, for my Lean project I was able to work on a cycle time reduction project at Chromalloy, another San Diego-based manufacturing plant (industrial turbine manufacturing). I chose this project as the company was most similar to my own, and each program participant has the opportunity to participate in such a project. You can choose to partner with another company that has similar (or different, if you prefer) processes, or bring your own project to work on!
Tell us more about your team project and what you learned from it.
Our Lean project was to enable Chromalloy to ramp production from a few dozen units per week to over 80 per week, by identifying choke points in production and eliminating inefficiencies (such as suboptimal batch sizes for key processes). I learned to implement the Lean tools such as value stream mapping, visual management, and spaghetti diagrams to identify the current state and identify the most impactful projects to improve the process. I also learned how to infer cycle times by counting the amount of material in between process steps, and comparing that to the processing time at each step.
How feasible is it to take this program while working full-time?
The Lean program is easy to take while working full time, as the classes occur during the workday once per week. You can then schedule the project work outside of your working hours in order to complete the class project.
Do you have any words of encouragement to those who would benefit from taking this program?
The cost of the program is pretty reasonable, so it’s really about working with your company to invest your time to attend the classes each week. I encourage anyone thinking about Lean to go ahead and do it — no matter what type of organization you work in, you can apply these principles and create an attractive return for your company as a result of your participation in the program.
Do you find yourself applying Lean principles in your everyday life?
Lean is also applicable to everyday life. Most simply, you can gain efficiency in anything you do by ensuring that the critical steps in a process are completed first, so that other time-consuming processes can be completed as soon as possible. For example, when preparing a meal, first do everything you need in order to get the main dish in the oven. While that process runs, you can finish any other non-critical tasks such as prepping the side dish or setting the table.
Also, I like to try and eliminate unnecessary motion using 5S (Lean term for organizing an area) principles for organizing tools. Staying with the kitchen example, organize it so that the most common things you use are concentrated in the center of your workspace, and items you rarely use can be put in the corner cabinet or in the garage (if you have a kitchen as full of cooking equipment as mine)
What did you want to be when you grew up?
I have been fortunate to have always had a clear vision of what I wanted to do with my career — my uncle got his electrical engineering degree from the University of Washington and then transitioned into management and had a successful career at Intel — eventually managing the strategic relationships with all of Intel’s software partners (Microsoft, Google, etc). So, I followed that path pretty much exactly — getting a technical degree and engineering background, and then transitioning to management. I also added an MBA to enhance my career prospects which has been extremely beneficial.
Anything you’d like to add?
I’ve been fortunate to participate in many continuing education opportunities through Cymer —including APICS CPIM certification (inventory and production management) and Six Sigma. But of all those, Lean at SDSU has been my favorite. The principles can be used every day once you have a working knowledge of the Lean tools. Plus, in my opinion it has the best return on the amount of time invested — in just a semester you can build this foundation and carry it with you throughout your career.